Commercial Metal Stud Framing
Get a quote
Let us know your requirements below and we’ll get back to you as soon as possible.
"*" indicates required fields
At RRS Enterprises LLC, we provide top-of-the-line metal stud framing services. We are proud to offer custom solutions and specialize in the highest grade components that meet or exceed local building codes standards. Our team has direct experience with various type of buildings, from hospitals and schools to airports and shopping centers.
Our metal stud framing will add both form and function to any space while providing superior strength and durability that can handle whatever your design plans require. With us, you can rest assured knowing your job is being handled by experienced professionals who understand why quality is important when it comes to this kind of workmanship.
Get started now on your next construction project with our high-quality metal stud framing services!
Contact RRS Enterprises LLC today for more information about how we can help bring your vision to life!
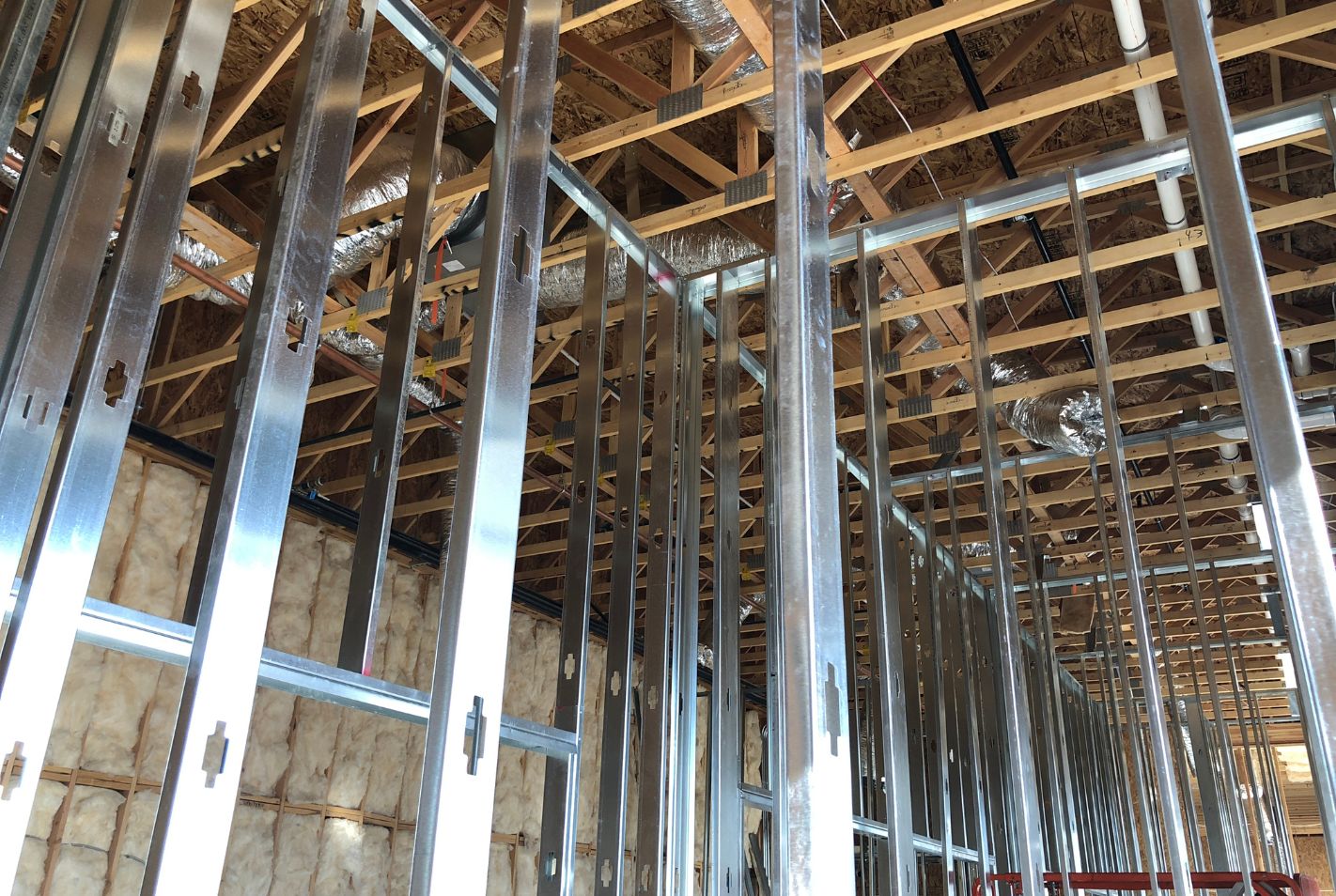
Let's chat about what possibilities exist for transforming your space!
Commercial Metal Stud Framing Contractor
OR CALL 800-432-5112
Metal Stud Framing FAQ
Metal stud framing is typically installed using a few basic tools and materials. First, the wall layout needs to be determined and marked on the floor or ceiling. This layout includes measurements for each wall section, such as length and width, as well as any openings like doors or windows. Once this is established, metal studs are cut to size and attached to the floor or ceiling through the use of a metal track, which is then secured with screws. The next step is to attach the studs horizontally between each wall section using fasteners like nails or screws. After this, the drywall panels can be hung on top of the studs and secured in place using more screws. Finally, any electrical wiring and insulation can be installed as needed before the drywall is taped and mudded. Once this is finished, the wall is ready to be painted or wallpapered.
For more complex walls, such as those with archways or other unique features, extra steps may need to be taken to ensure a level and secure installation. For example, the wall framing may need to be adjusted or extra support added in order to create a level wall surface that is strong enough to hold the drywall and other materials. In some cases, steel or wooden lintels may be used in place of studs for increased stability.
No matter what type of wall is being built, following proper installation techniques is essential to ensure the wall’s strength and longevity. Drywall should be securely fastened with screws at regular intervals, taking into account the size of the drywall panels and their weight. Taping and mudding corners and seams should be done in two passes, allowing ample drying time between applications.
Metal stud framing offers a number of advantages over traditional wood or brick-and-mortar construction methods. Firstly, metal studs are lighter and easier to install than traditional building materials, allowing for faster completion times on projects. Additionally, metal studs are fireproof and provide superior structural integrity compared to traditional materials. This makes them ideal for use in homes, commercial buildings, and places of worship that need to be fire-resistant. Additionally, metal studs are also resistant to moisture damage and insect infestation, making them a better choice for many applications. Finally, they are Eco-friendly since they can easily be recycled or reused. Metal stud framing is cost-effective and provides superior strength and durability compared to traditional materials, making it an ideal choice for any construction project. With its ease of installation, fireproof qualities, resistance to moisture damage and pests, and Eco-friendly nature, metal stud framing is quickly becoming the go-to choice for many contractors.
Metal stud framing must meet the fire rating requirements of the applicable building code. Generally, this means that metal studs must be able to resist heat and flame for a certain period of time, typically ranging from 45 minutes to 3 hours depending on the project’s needs. To achieve this, metal studs may need to be lined with fire-resistant materials such as drywall, gypsum board, and spray-on fireproofing. Additionally, fire stops may need to be installed in the framing to limit smoke and flame spread. It is important to check with local building codes for specific requirements in order to ensure proper fire safety.
Metal studs can also have a Class A, B, or C fire rating. Class A is the most fire-resistant rating and requires that metal studs be made from special materials such as fiberglass, steel, or gypsum board that are designed to resist heat and flame for longer periods of time. Class B and C ratings are generally less stringent and may require only basic fire-resistant materials such as drywall and fire-rated insulation.
When it comes to fire safety, the most important thing is to understand what local building codes require for a particular project. By following these guidelines, you can ensure that your structure meets all necessary requirements for fire safety. Additionally, properly installing metal studs according to manufacturer instructions ensures that the walls and ceilings are properly sealed. Properly sealing any joints between materials can also help reduce the risk of fire spread. Finally, using proper fireproofing products on combustible items such as furniture or wiring helps to protect your investment in case of a fire emergency.
Metal stud framing must meet the seismic requirements set forth in the International Building Code (IBC). These requirements include:
• Securing metal studs to their base plates and ceilings using fasteners that are designed for seismic activity.
• Using a minimum of two fasteners at each connection point when attaching metal studs to masonry walls.
• Making sure the metal studs are properly braced in order to resist seismic loads and lateral forces.
• Incorporating additional features such as stiffness ties, anchorage straps, and triangulated wall bracing.
• Using metal studs that meet the standards set forth by ASTM C 645 or AISI S100.
• Ensuring a minimum of two layers of gypsum board are used on either side of each partition wall, ceiling, and floor-ceiling assembly to help absorb seismic energy.
•Installing a minimum of one layer of gypsum board on the interior side of all exterior walls.
•Using Type X or better gypsum board to help protect against the spread of fire.
•Ensuring that each ceiling is adequately braced and secured with fasteners to resist seismic forces, in accordance with local building codes.
•Installing seismic clips or anchors at intersections between walls and ceilings/floors, as well as around fixtures and equipment in the ceiling area.
•Using horizontal anchorage straps on all interior partition walls to resist lateral forces due to seismic activity.
• Installing additional bracing along the length of exterior walls, at door and window openings, and in the corners of any non-load-bearing walls.
• Enforcing minimum deflection requirements for floor joists or ceiling trusses according to local building codes.
• Installing vapor barriers to protect against moisture damage, either with 6 mil polyethylene sheeting or an approved alternate material.
• Inspect the structural framing for signs of damage or deterioration, such as warping, cracking, or rotting of wood members.
• Verifying that all connections between frame components are adequately secured and free from any visible defects.
• Installing a minimum of two inches of insulation in exterior walls and attics, as well as all floors located above unconditioned spaces.
• Applying fire-resistant sheathing to walls and ceilings in the form of gypsum board or other approved material.
• Installing weatherproofing materials such as flashing around windows and doors, caulking around baseboards and trim, and vapor barriers on the exterior face of walls.
• Inspecting for termite damage, ensuring that any such damage is treated and all existing colonies are eradicated.
• Ensuring that any damaged or deteriorated materials, such as roofing shingles or flashing, are replaced with new materials.
• Installing gutter systems to divert rainwater away from the home’s foundation.
• Ensuring that all electrical and plumbing systems are up-to-code and properly installed.
• Installing appropriate safety features such as smoke detectors, carbon monoxide detectors, and fire extinguishers.
Metal stud framing, also known as light gauge steel framing, is a construction method where metal studs are used to support the walls and ceilings of a building. Metal studs are thin metal frames that come in various lengths and widths. They can be quickly put together with specialized tools to form walls and ceilings. This type of framing is becoming increasingly popular due to its affordability, durability, and versatility.
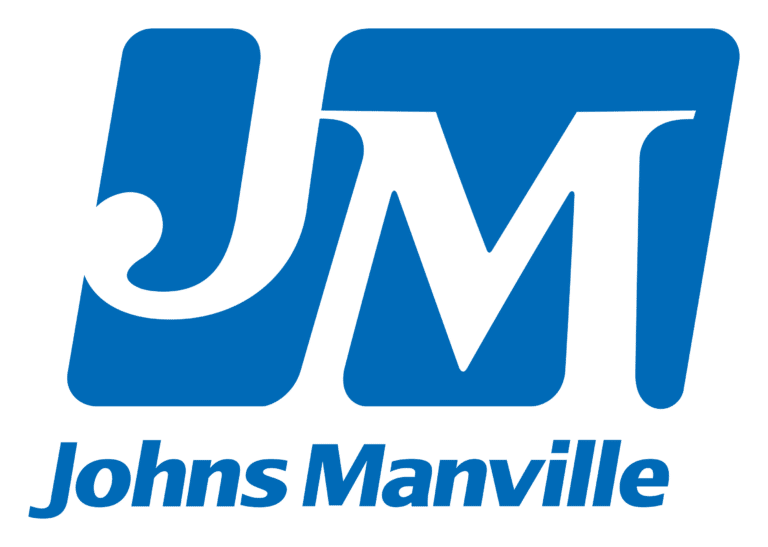
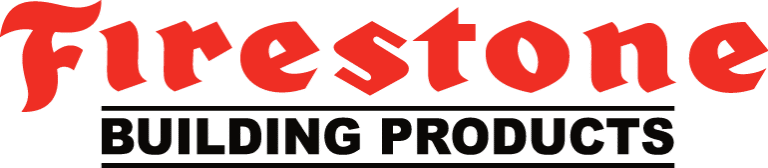
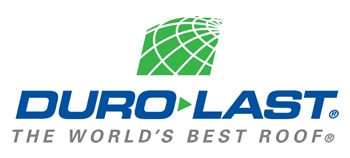
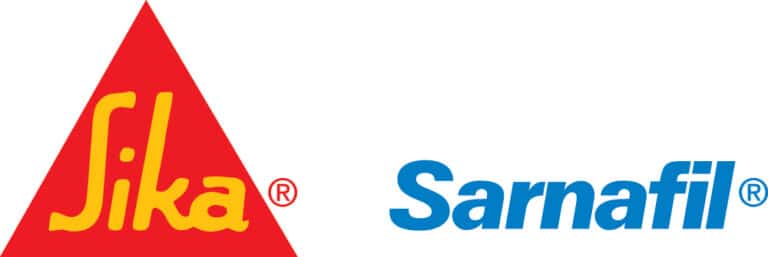
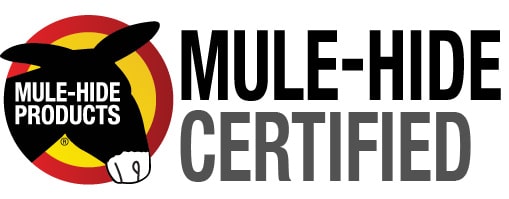
Let's chat about what possibilities exist for transforming your space!
OR CALL 800-432-5112